10 falhas que podem ser identificadas com o Alinhamento a Laser
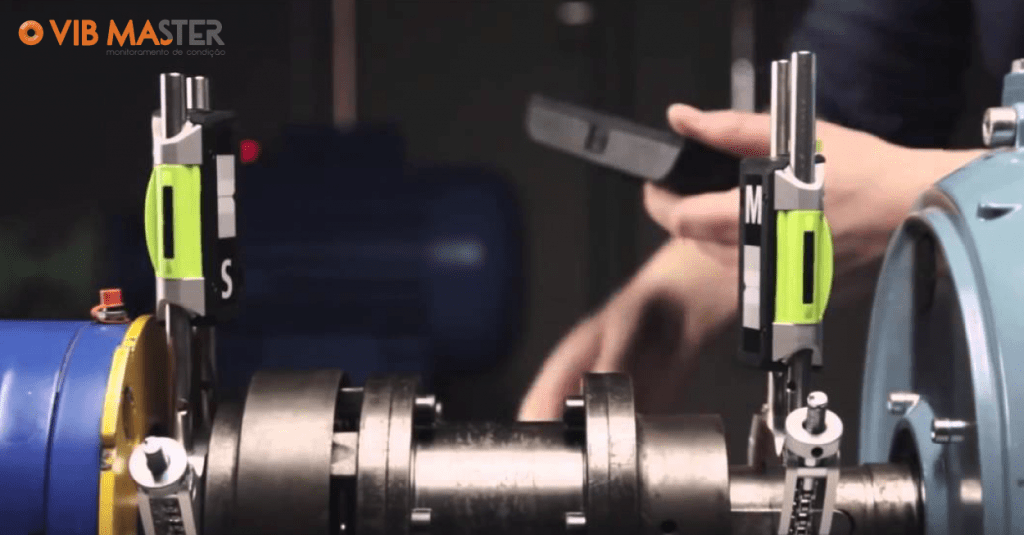
O alinhamento a laser é um processo de manutenção industrial, extremamente eficiente e necessário para manter as condições ideais de operação do equipamento, reduzindo custos desnecessários e ampliando a confiabilidade disponibilidade do conjunto mecânico no campo fabril, dois grandes indicadores e responsáveis pelos resultados no setor.
Neste artigo, você verá:
- A importância do alinhamento dos equipamentos
- Tipos de desalinhamento
- Como a tecnologia pode ajudar neste processo
- 10 falhas que podem ser identificadas com o alinhamento a laser
O alinhamento dos equipamentos, é um processo de manutenção industrial muito importante para o desenvolvimento das atividades no campo fabril, pois, os equipamentos necessitam estar alinhados geometricamente e nivelados para operarem de forma adequada, com máximo de eficiência e o mínimo de desgaste possível.
A importância do alinhamento dos equipamentos
A não identificação de pontos desalinhados, e claro, a tomada de ação para a correção imediata dos mesmos, podem comprometer a estrutura do equipamento e trazer prejuízos não somente para a capacidade de produção, mas também para a gestão de custos do setor de manutenção.
Segundo estudos realizados e divulgados pela Abraman (Associação Brasileira de Manutenção), principal órgão regulador das atividades no país, equipamentos desalinhados podem consumir até 15% a mais de energia, por exemplo. Mas, este não é o único problema que pode ser identificado.
Tipos de desalinhamento
Podemos classificar os tipos de desalinhamento em dois: angular e radial, ou em três, angular, radial e ambos, juntos.
Desalinhamento radial
O desalinhamento radial, também conhecido como desalinhamento paralelo, consiste na distância incorreta entre as duas linhas centrais do eixo, em qualquer ponto, tanto no plano vertical, quanto no horizontal.
Desalinhamento angular
O desalinhamento angular, que também recebe um segundo nome, neste caso, axial, consiste na distância incorreta e diferente entre as duas extremidades do eixo, formando uma linha em diagonal em um dos lados, ou em ambos. Também é possível identificá-lo no plano vertical, como no horizontal.
Como a tecnologia pode ajudar neste processo?
O monitoramento de condição, tem como objetivo identificar a raiz de possíveis falhas, permitindo que a equipe de manutenção realize a correção das mesmas, através de um processo de manutenção preventivo, antes mesmo de suas consequências, como quebras e paradas não planejadas.
Neste caso, ou seja, no desalinhamento dos equipamentos, o monitoramento de condição traz com base a tecnologia, na realização do alinhamento a laser de eixos.
Sendo os pontos de desalinhamento a raiz de inúmeras falhas, podemos afirmar que o monitoramento de condição e o alinhamento a laser de eixos podem se tornar os maiores parceiros dos gestores na busca por identificá-los e corrigi-los.
10 falhas que podem ser identificadas com o alinhamento a laser
Com a aplicação do alinhamento a laser, é possível identificar problemas comuns que afetam os conjuntos mecânicos e prejudicam os resultados no setor. Por isso, separamos 10 deles, para que você possa entender os benefícios desse processo de manutenção e a importância dele para a sua empresa.
- Desgaste precoce de mancais, rolamentos, engrenagens e correias
- Registro de vibração irregular
- Parafusos e peças soltas
- Trincas nas bases e suportes
- Pé de motores mancos
- Acoplamentos com folgas
- Carcaças torcidas
- Vazamentos em flanges de tubulações
- Imprecisões de montagem de sistemas mecânicos
- Alto consumo de energia
O desalinhamento dos equipamentos possui uma ligação direta com o consumo de energia e reações térmicas irregulares. Como vimos, no início deste texto, equipamentos desalinhados podem consumir até 15% a mais de energia. Já estudos minuciosos têm documentado uma economia de energia de 3 à 8%.
Desta forma, podemos perceber e entender a dimensão dos benefícios trazidos com a implementação do monitoramento de condição, e neste caso, com a estruturação de rotinas de manutenção como o alinhamento a laser, na busca pela minimização de falhas e quebras e a ampliação da confiabilidade e a disponibilidade dos equipamentos no campo fabril.
Saiba mais sobre os alinhadores de eixos e polias ou sobre o serviço de alinhamento a laser oferecidos pela VibMaster.
1 Comentário
Os Comentários estão Encerrados.